www.obiuan.net
Costruzione della scocca
per MikroBot
Vediamo ora come costruire il
pezzo portante del robot la scocca. Su questo pezzo
come abbiamo già detto verranno assemblati tutti i particolari. Per realizzare la scocca è necessario
innanzi tutto avere un disegno quotato per eseguire
le varie operazioni richieste. Ora...Visto che non tutti
hanno conoscenze di disegno tecnico ho studiato un metodo per
la sua realizzazione.
Si
tratta di scaricare questo file (clicca quì
per visualizzarlo). Procedere ora come segue.
Salvare
l'immagine su disco fisso. Aprirlo ora usando il Paint
di windows. Stamparlo ora al 51% della sua dimensione
originale. A disegno stampato, controllare con un righello
che le quote del rettangolo siano 75x50 mm. Il disegno rappresenta lo sviluppo in
piano della nostra scocca. In fig. 1 potete consultare il
disegno quotato in mm.
|

Fig. 1
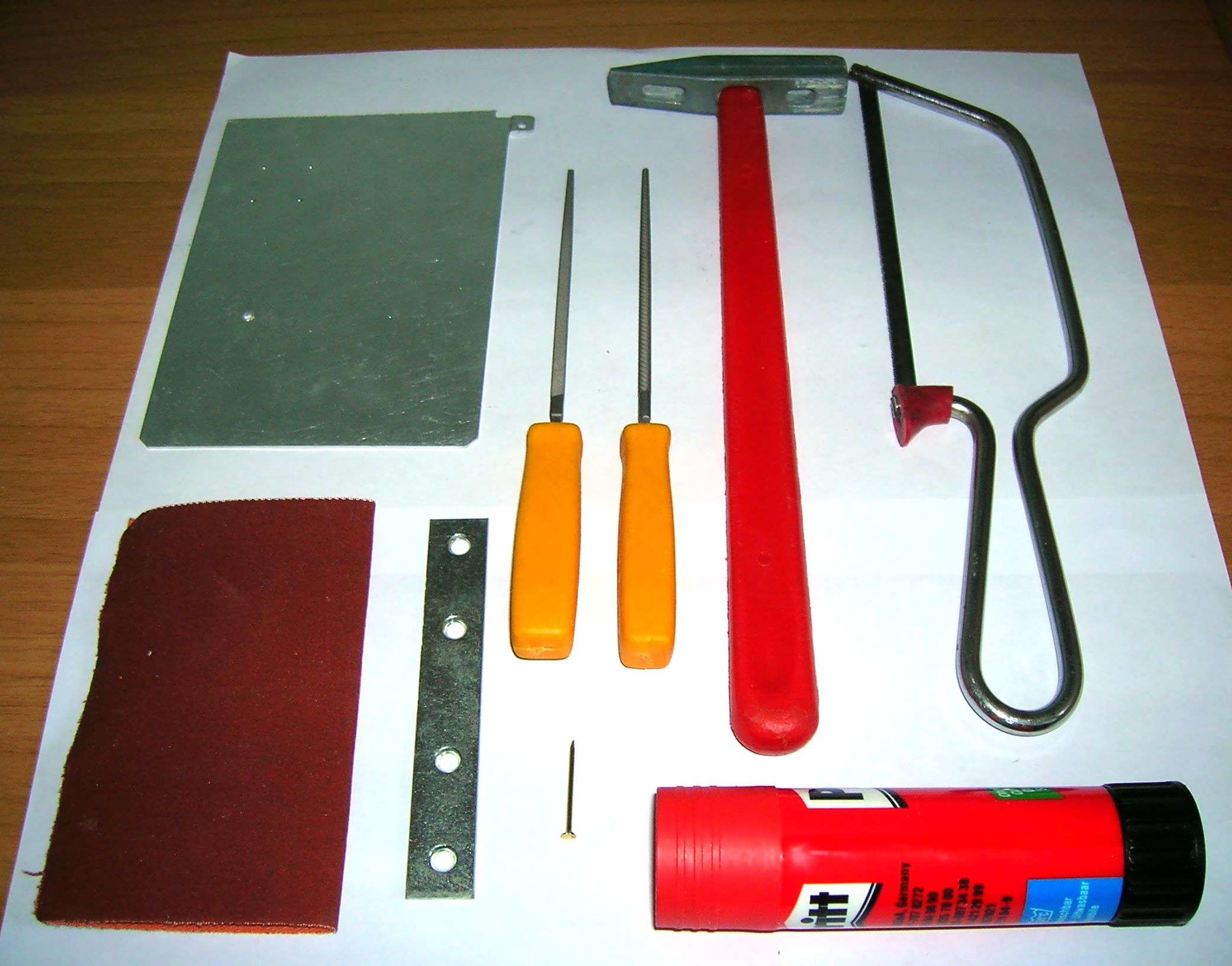
Fig. 2
Come per tutte le altre parti costruite
fin'ora vediamo in figura 2 il minimo di attrezzatura
necessaria per costruire il nostro particolare. Un pezzo
di alluminio 70x50 spesso 1 mm, una morsa, un
seghetto, punte da 1 - 2.2 e 4 mm, una limetta da
ferro quadrata 4 x 4mm, un pezzo di ferro con un lato
diritto che utilizziamo come guida per il taglio della
forma, un trapano (meglio se munito di colonna) e tela
smeriglio fine per rimuovere sbavature causate da taglio
e foratura.
|
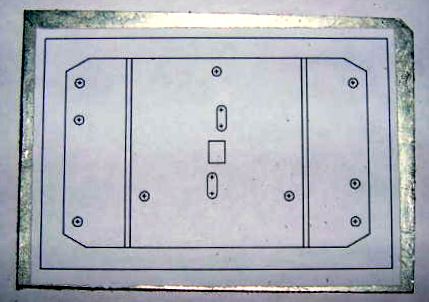
Fig. 3
In fig. 3 vediamo il disegno che dobbiamo
stampare su un normale foglio di carta. Tagliare il rettangolo
e incollarlo con della comunissima colla stik sulla
nostra basetta di alluminio spesso 1 mm. Lasciarlo
asciugare. Una volta asciutto la prima cosa da fare è
eseguire tutti I fori disegnati utilizzando un trapano
(se dispone di una colonna meglio ancora). Prima di forare
bisognerebbe bulinare ciascun foro al centro. Si può
allo scopo utilizzare un chiodino di acciaio inox appuntito e
un martello (occhio alle dita...).
|
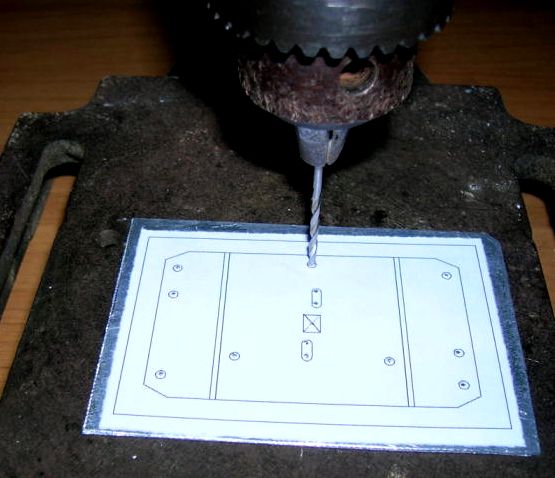
Fig. 4
Iniziamo ora a fare I fori utilizzando
una punta piccola da 1 mm e sucessivamente finire
le forature utilizzando le punte richieste. Il problema
principale della foratura senza colonna è che la punta
tende sull' alluminio a scivolare ecco perchè la bulinatura
si rende necessaria. Utilizzando una punta piccola anche
meno di 1 mm la bulinatura accompagna la punta nella
sede del foro richiesto. In fig. 4, vediamo la piastra
in fase di foratura.
|
Fig. 5
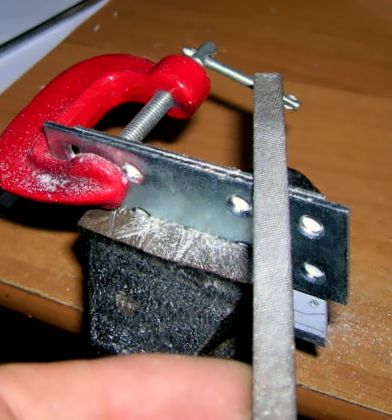
Fig.
6
Eseguita la foratura il passaggio sucessivo
è il taglio. Come per le basette dei circuiti stampati
anche per la scocca utilizzeremo lo stesso metodo per
il taglio. Prendere il pezzo di metallo diritto posizionarlo sulla scocca in
corrispondenza di una riga stringerlo sulla morsa ed effettuare il taglio (vedi
fig. 5). Procedere allo stesso modo per I sucessivi tagli fino ad avere Il
pezzo come in fig. 7. Attenzione fino a questo punto della lavorazione a non
rimuovere il disegno incollato per nessun motivo. Un
consiglio. Prima di rimuovere il pezzo dalla morsa, è
consigliabile correggere le imperfezioni del taglio
utilizzando una limetta piatta fig.( 6). La riga metallica
di guida, ci aiuterà a rifinire il profilo dopo
il taglio. Eseguire le stesse operazioni per ciascun
lato.
|
Fig. 7
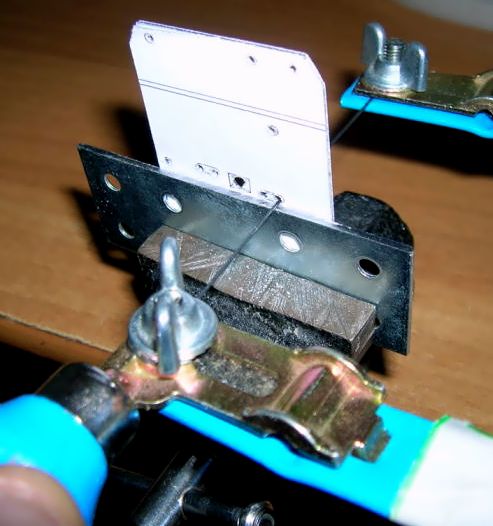
Fig.
8
Si tratta ora di sagomare il rettangolo
centrale per I connettori dei motori e le asole di regolazione
dei motori. La sede dei connettori bisognerebbe sagomarla a seconda
del tipo di usato. Modificate quindi la sede relativa
per quelli che avete a disposizione. Eseguite ora le due asole utilizzando
prima un archetto da traforo per tagliare il materiale residuo
e poi usare una limetta tonda per rifinire le asole. (fig. 8).
Tali asole serviranno per regolare i due porta
motori e l'oring relativo per la trasmissione del moto. Eseguito il taglio, bisogna con tela
smeriglio sagomare i lati da imperfezioni. L'importante
è non oltrepassare la riga di riferimento di ciascun
lato. Se succede di tagliare più del dovuto non pregiudica
il funzionamento ma l'estetica ne risente. L'ultima operazione la più delicata è la piegatura
dei due fianchi laterali. La piegatura la ritengo delicata per ovvi
motivi di stabilità della struttura.
|
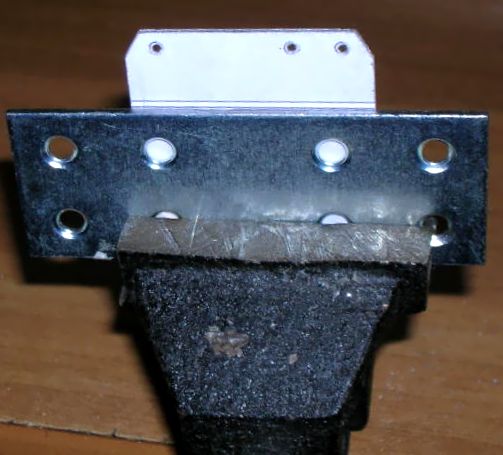
Fig. 9
Il metodo più semplice che ho studiato
per eseguire la piegatura dei due fianchi è quello visualizzato
in fig. 9. Si tratta di utilizzare il solito righello
di ferro diritto già utilizzato per il taglio della
scocca e farlo coincidere con la linea di mezzeria interna, dove
verrà eseguita la piegatura. Posizionare ora il gruppo
su una morsa (che abbia le ganasce diritte) e bloccare
il tutto senza esagerare però trattandosi di aluminio.
Una
volta sicuri del posizionamento, poggiare I due
pollici sul lato da piegare e eseguire la piegatura di 90°.
Il disegno deve restare
all' interno della piegatura e non all' esterno. Procedere allo stesso
modo anche per l'altro fianco. Utilizzare se la disponete una squadretta
per verificare il corretto angolo di piegatura (90°). Naturalmente
I 4 fori che porteranno I due alberini devono essere stati eseguiti
in asse altrimenti solo 3 delle quattro ruote toccheranno il suolo.
Comunque...
ho fatto in questo modo 3 scocche e tutte hanno dato esito positivo.
Ora
potete rimuovere il disegno semplicemente bagnando la carta. Asciugate
la scocca e con la tela smeriglio lucidate e asportate le imperfezioni.
I
fori molto probabilmente dovranno ancora essere ritoccati. Lo vedremo
in seguito però.
|
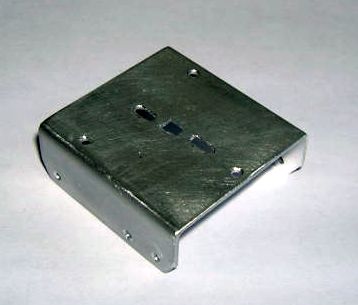
Fig. 10
In fig.9 vediamo come appare la scocca
quasi ultimata. Dico quasi perchè bisognerà ancora
ripassare I fori manualmente con le punte e adattare
I due conettori che portano alimentazione ai motori.
Queste
operazioni le vedremo in fase di assemblaggio nella
sezione assemblaggio parte meccanica. Per ora poniamo
la scocca assieme alle altre parti costruite fin'ora e
passiamo ai pezzi sucessivi.
|
  
I contenuti di questo
sito sono per uso didattico e/o amatoriale. L'utilizzo
commerciale non è consentito. L'autore declina ogni
responsabilità per danni arrecati a cose e/o persone
in conseguenza alla realizzazione e/o all'uso dei progetti
presentati in questo sito.
|
|